
Considerations When Planning A Reprocessing Project or Renovation
Your department has gotten the greenlight to conduct a large project or renovation; Congratulations! It’s an exciting opportunity and there are probably a ton of ideas bouncing around in not only your head, but the heads of everyone in your department. Projects and renovations don’t happen every day, and this is a chance to make meaningful changes your department has likely wanted (and needed) for years.
You as a leader want to maximize the benefit of this project, so what are some considerations to keep in mind as you begin planning?
Equipment
If you’re like many departments throughout the United States, you probably have aging sinks and tables that weren’t originally designed for use in a reprocessing department. Your decontamination sink might be suited for a restaurant!
There are a few things to keep in mind when starting your research on equipment:
- Height adjustability: With teammates of varying heights, it can be difficult to find the right height for sinks & tables and create a comfortable working environment. The best way to remedy this concern is ensuring that your new equipment is height adjustable, and that the method of lifting and lowering is reliable. No one wants downtime because their sink or table’s lifters need to be repaired! Try seeking out reputable lifters that are electro-mechanical; hydraulic lifters may be cheaper up front but can incur years of service costs.
- Ergonomic features: Height adjustability is a great start to improving ergonomics for your team, but there are other ergonomic considerations as well. Reducing pinch points with wrist rests, ensuring materials and tools can be easily reached, and that the depth of your basins is adequate for the work being done, but don’t require reaching or hunching, are all important considerations.
- Quality & longevity: Large investments in reprocessing departments don’t come around very often, so it’s important to implement equipment solutions that will last for the long haul. Fabrication and build quality, as well as component reliability, are two key aspects of longevity that need to be top of mind; you don’t want to be replacing your equipment after 3-5 years!
Workflow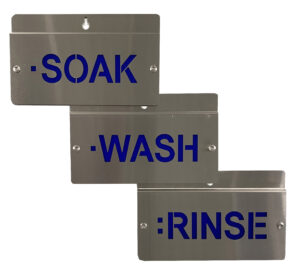
Equipment in reprocessing departments serves as an engine for activities and productivity; many aspects of reprocessing revolve around them. For this reason, it’s important that the workflows built around sinks or tables are dynamic and optimized for the needs of your department.
- Pegboards: Pegboards on sinks and tables should almost be considered mandatory when planning your project or renovation, and with good reason! Pegboards allow you and your team to not only consolidate tools and materials right where they’re needed, reducing time spent away from the sink and table, but also configure them in a way that streamlines workflow and makes it easier for your team to accomplish their tasks. Some hinged pegboard options for reprocessing sinks can allow re-organization of accessories to further tweak workflows.
- Workflow plates: Mounted on pegboards, workflow plates clearly identify which basins should be used for which activity at a reprocessing sink. This helps teams organize their workflows more clearly, help ensure compliance, and demonstrate the thought put into your processes in the event of a visit from the Joint Commission.
Space Limitations
With the opportunities a project or renovation present, you don’t want to miss out on the ability to make necessary changes because of unique spatial constraints in your department. Identifying a
partner that is able to offer you options based on your needs will give you the flexibility to get exactly what your department requires while the window of opportunity is open.
- Various sizes: A partner that offers a variety of sink and table sizes will help you get the right tool implemented quickly if you’ve got room for a standard-sized sink or table. The more standard sizes available, the higher the likelihood of identifying a good fit quickly.
- Custom configurations: If your department has limited or unique spatial considerations, a partner that’s able to develop custom-sized tables or sinks to fit your space is exceptionally beneficial. This doesn’t just mean being able to build very big or very small, it’s about the ability to create sinks or tables in the odd, in-between sizes to make sure that the space your department does have available to it is used to its maximum potential. This can also mean custom configurations for basins, shelving, feet, and other equipment features.
Conclusion
While this is certainly not an exhaustive list of considerations when planning for your large project or renovation, it does serve as a great starting point and lens to assess your options through. Making sure that you’ve identified your needs and unique departmental circumstances up front will help you move through your project or renovation process more smoothly, as well as maximize the benefit to your department upon completion!
Want to bounce some ideas around or get an outside perspective on your project? We’d love to help!